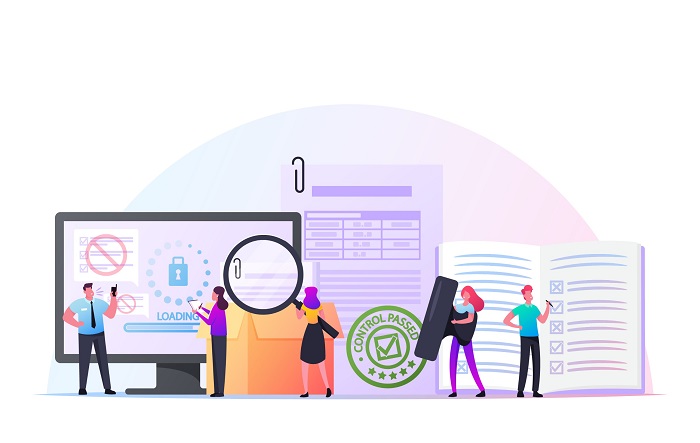
Many businesses have safety programs, but does that establish a safety culture? Adi Klevit recently asked that question of Joshua Keene, Account Executive at LaPorte Insurance.
During their discussion, Adi and Joshua talked about the difference between a safety program and a culture of safety - and Joshua shared how a business can build a process to weave safety-minded actions into everyday activities. Business owners who have worked to create an authentic safety culture reap the rewards with fewer worker's comp claims, reduced service interruptions due to hacking or malware, and increased brand recognition for their safe practices.
Read on to find out what you can do to build a safety culture in your business.
What is a safety culture?
There is a difference between a safety program and a safety culture.
A safety program is something your HR team or business leadership writes down to help them lower insurance costs. It may be something they’ve shared with the team - or it might live on their hard drive without ever being shared. They may have a meeting or two about it - or employees may know nothing about this program.
Safety culture is something that involves all of your employees. They know about it and are involved in maintaining the reputation and safety of the business. Entry-level employees to the CEO practice what they preach - and safety is at the top of mind in the company.
This type of culture-wide safety consciousness is the best way to reduce accidents and gain a sterling reputation. Utilizing the best practices listed in the last section of this article not only helps to build this culture but will also show your employees and customers that you genuinely care about their well-being.
Consider these common safety issues.
When one says “safety program,” one usually thinks of contractors or OSHA compliance. While this type of risk mitigation is vital, modern companies face other safety issues. Consider this list of typical safety problems that harm businesses, employees, and customers alike:
- Computer security
- Phishing
- Hiring/firing practices
- Harassment policies
- Disease mitigation
- Indoor air pollution
- Mold concerns
- Building maintenance issues
- Accessibility challenges
- Poorly placed or lit parking
- Equipment concerns
- Weather-related issues
- Ergonomics
- Licensing
- HIPPA compliance
- PCI compliance
- OSHA compliance
- And more
These and many others are issues that most businesses could encounter - and they are risks worth mitigating.
The process behind a safety culture
Because safety is part of the fabric of your business, a process needs to be built to ensure appropriate gear is ordered and distributed, maintenance happens consistently, safety meetings occur, and more.
Here are three critical components for developing a safety culture:
1. Establish a safety committee.
Your committee can be any size, but it should include all employment levels and each department. If you have a shipping department, fabrication department, sales department, and HR, all should be included in the safety committee.
2. Establish a charter.
The first step for a safety committee is to write clear goals and then delineate what it will take to accomplish them. These goals need to be measurable with metrics that can be obtained and tracked.
3. Build processes to ensure safety is kept at the top of mind.
A few examples of how this can be done include safety as part of job listings, initial and continuing safety training, consistent computer updates, continual building maintenance, and safety incentive programs.
Processes can be established for your safety culture that gradually turns safety from something your team rarely thinks about to an everyday occurrence. The exact procedure will depend on what is included in the charter, but overall, you can follow the following steps for process building:
1. Find out what safety actions are already in place.
Document them along with any related policies, processes, and procedures.
2. Fill in the blanks.
Now that you know what is in place, you can compare this to your established charter. What is missing? You and your committee will need to build new processes to implement these policies.
3. Run through all of the processes now documented.
Evaluate if they work and if they achieve the desired goal. If not, review the steps and find out what’s missing.
4. Revisit these processes every few months.
As your company becomes more safety-conscious, review the processes to see what needs to be updated and what can be improved.
Are you hoping to build processes that have safety in mind? Get in touch with Business Success Consulting Group! Our process experts will provide the foundation you need to develop safety-conscious processes.